Result
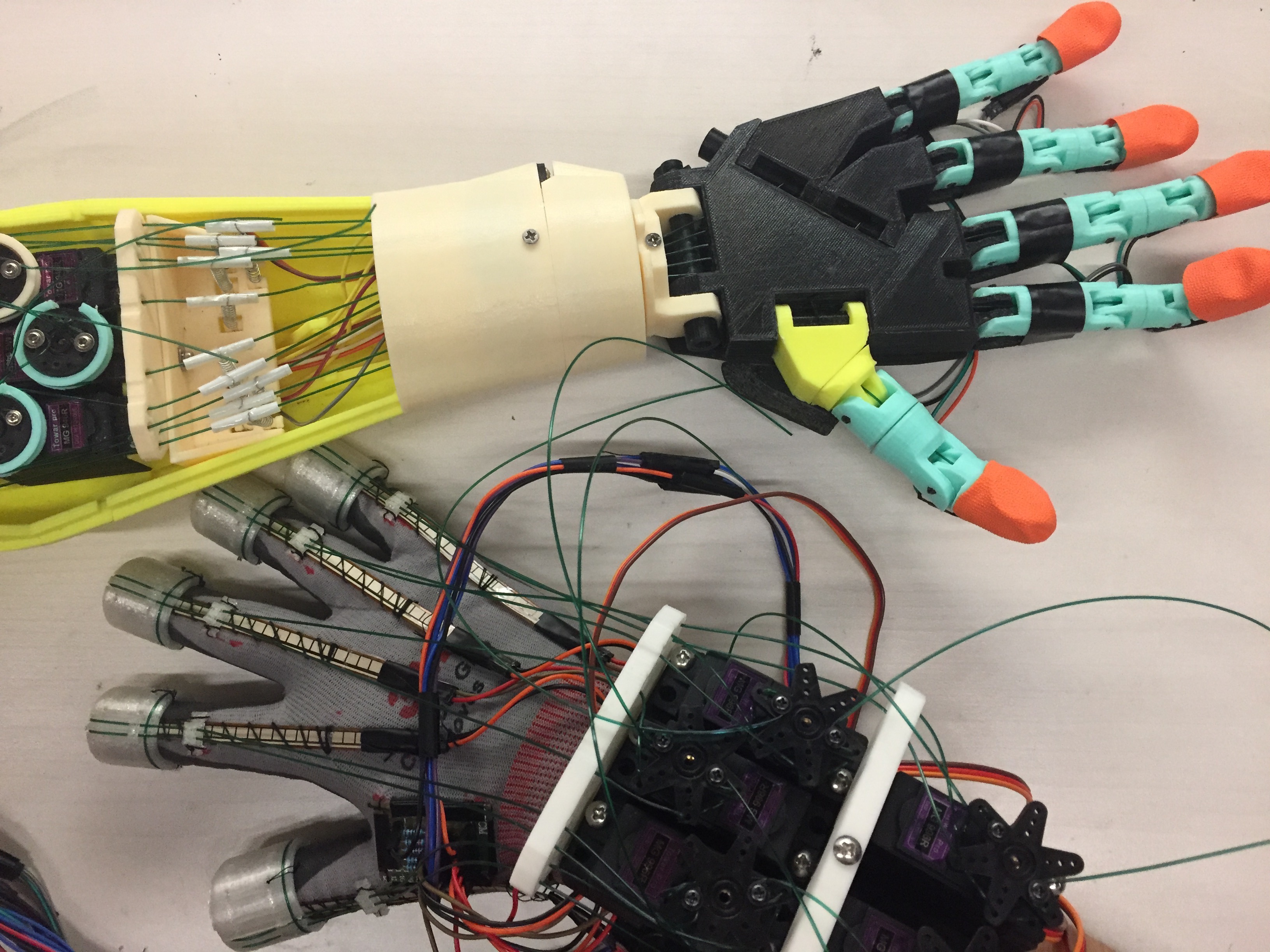
At the end of this FYP, a robotic hand that can be controlled by sensor glove and able to provide haptic feedback has been made successfully. It has an around 0.2s delay between user moves his/her hand and the robotic hand response by mimic the user’s gesture. The delay can be noticed but it is acceptable and does not affect the whole user experience a lot. The delay is mainly due to the rotating speed of the servos. Because of the strong torque that is provided by the wire and the good strength of the wire, this robotic hand can lift heavy object up to 2kg. However, since only the fingertips of the robotic hand are linked to the servo. There are no individual servos for controlling the knuckles. The fingers are crooked just relying on the tension of the wire.
to the rotating speed of the servos. Because of the strong torque that is provided by the wire and the good strength of the wire, this robotic hand can lift heavy object up to 2kg. However, since only the fingertips of the robotic hand are linked to the servo. There are no individual servos for controlling the knuckles. The fingers are crooked just relying on the tension of the wire.
For the haptic feedback, user’s can experience a significant pulling force when pressure sensor of the sensor glove is being pressed. This make the user can roughly feel the object that the robotic hand is gripping. If the user tries to resist the pulling force and keep moving, the pressure detected by the pressure sensor will be higher and apply a larger pulling force to the user’s finger. However, the tension of the wire is affected by many factors including the position of the servo bed and the angle of the wrist. This make calibration difficult and user’s have to maintain steady to achieve realistic haptic feedback.